News
Precise and reliable Metal detectors from Mesutronic protect the processing machines of the industry giant Stora Enso
Somewhere on a round timber yard in South Germany: a gripper places a tree trunk on a conveyor belt, which guides it through a metal detector. Suddenly an alarm siren sounds and the conveying process is stopped – a piece of metal has been detected. This, or something similar, is the common metal detection process in the wood industry. Possible metal contaminants often have to be intercepted before cutting in the sawmill in order to protect the expensive saw blades. But what about the protection of machines in the further processing? The Finnish industry giant in the wood segment, Stora Enso, has relied for years on the proven technology from Mesutronic GmbH from Kirchberg im Wald to protect its production machines. But first things first!
The Stora Enso company can look back on a hundred years of history and is today one of the largest timber processors worldwide. Its five business divisions generate an annual turnover of around 10.3 billion euros with a total of 28,000 employees. The ‘Wood Products’ segment is one the most successful in the company and is really impressive with a sawing capacity of 5.6 million cubic metres. Part of the Stora Enso family is located in the picturesque town of Pfarrkirchen in Lower Bavaria. This location mainly produces KVH® solid structural timber and Duobalken/Triobalken® beams for the construction industry. Naturally the production also generates waste – the so-called industrial wood residues. These are woods generated as by-products, residues or waste in the woodworking industry. Of course the industrial wood residues are not simply disposed of in the Pfarrkirchen works, but are recycled in a sustainable and environmentally friendly manner. First of all the wood is collected in silos and prepared for the further processing. The first metal detector from Mesutronic is already installed before the collecting containers; it acts, so to speak, as the entrance inspection. It is mounted under a vibrating channel and has the task of detecting larger metal parts that could damage the downstream shredder. And it has been successfully doing just that for over ten years now. After the silo there are in principle two possibilities for further utilisation. Firstly, combustion in the in-house heating plant or, secondly, processing into wood pellets. In the latter case, further processing steps follow that require a great deal of care. The raw materials are ground further in a grinder and fed to the pelletizing plant via a piping system. Then, under high pressure, the material is pressed through a steel die, which has holes in the desired pellet size.
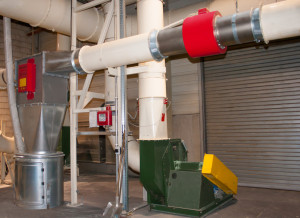
The METRON 05 PowerLine metal detector, in combination with the high-speed TEXREJECT, a highly efficient complete system
The high pressure heats up the wood and causes the lignin in the material to liquefy, so that it can act as a binding agent. In order to protect the die, a metal detector with a separation system must be placed before the pelletizing plant. Stora-Enso in Pfarrkirchen thereby utilises a solution from the textile industry. The Metron 05 PowerLine metal detector is combined with the high-performance Texreject separation system to form a highly efficient complete system. The metal detector is mounted in a piping system and checks the ground wood before the separating diverter. If a metal contaminant is detected, the detector sends a signal to the Texreject, which then separates out the contaminated material. The separation of the small fragments of wood in a controlled manner is both a big challenge and new territory in the wood industry. The separator from Mesutronic provides all the conditions required to overcome this difficulty. Thanks to the pneumatic diameter of 500 mm it can cope even with enormous streams of material without problems. With its fast flap opening time of 0.16 s it separates contaminants from the product stream reliably and without interruptions in production and diverts them into a bad material container. Contaminations that occur are, for example, the steel wedge hammers used for marking solid structural timber. These are so hard that they would irreparably damage the pellet die and bring production to a standstill. The reliable and low-maintenance metal detectors and separators from Mesutronic have been reliably preventing that for many years.