Cutting without a break – Increasing process reliability in sawmills with metal detectors at I.B.H. Sägewerk GmbH
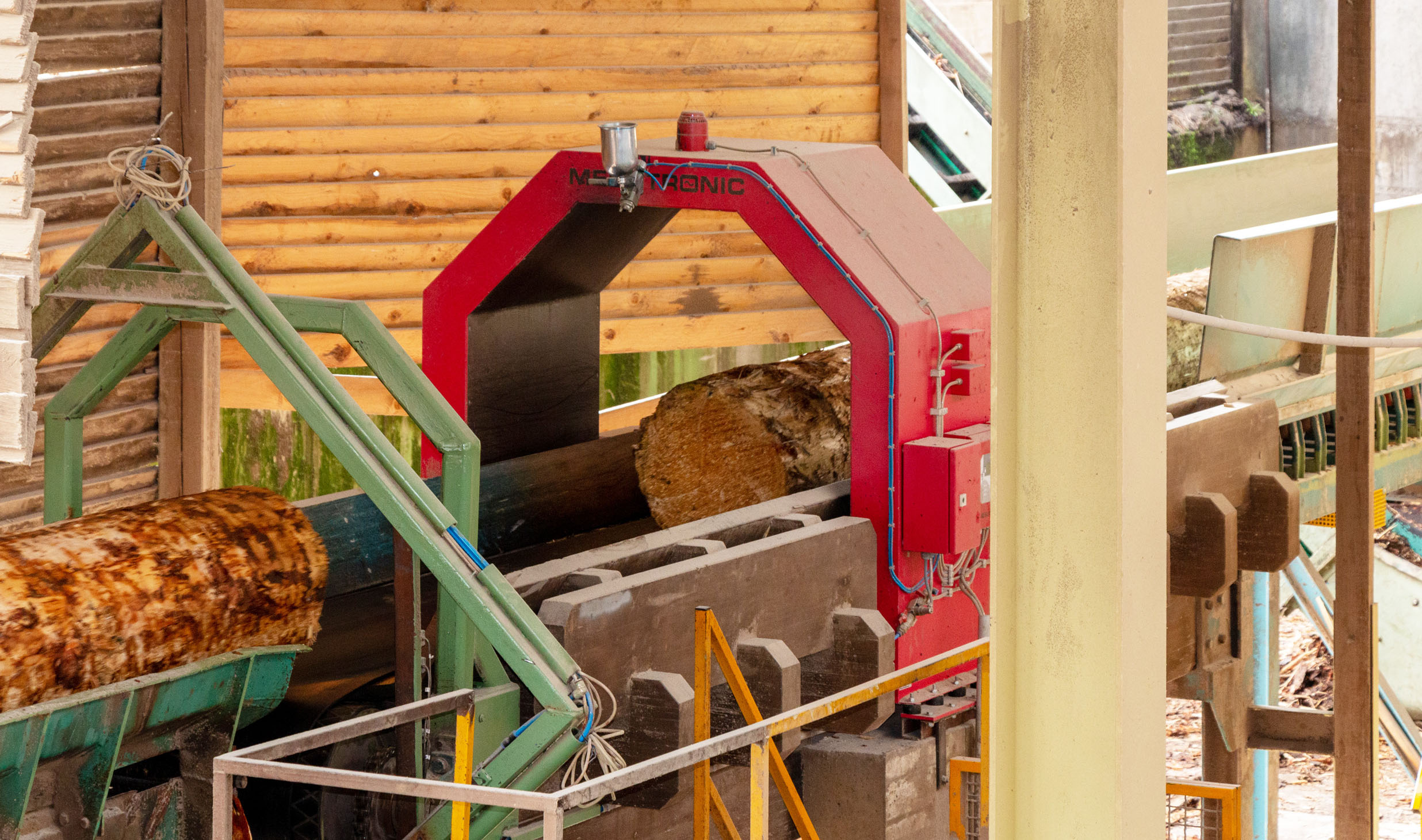
For the search for splinters in round wood, the metal detector METRON 05 CO is in use at Harperscheid
Cutting without a break – Increasing process reliability in sawmills with metal detectors at I.B.H. Sägewerk GmbH
Apart from hazards due to nails or fence pieces, burdens from the last war are still a problem when processing large logs. The handling of ingrown munition remnants is still part of the daily business of a sawmill on the German-Belgian border, even when processing softwoods. One such sawmill is I.B.H. Sägewerk GmbH in Schleiden. High-performance metal detectors are an indispensable protection mechanism here for productive wood cutting.
Growth on fertile soil
I.B.H.’s history began in 1996, when the works in the district of Euskirchen were taken over. Or, to be more exact, in the small village of Harperscheid as part of the town of Schleiden, which has a population of around 13,500. In these rural surroundings, in the midst of the Rhenish Massif, lie some of the largest forested areas of North Rhine-Westphalia and Rhineland-Palatinate: Hunsrück, Taunus, Westerwald or, directly outside the company’s front door, the Eifel. The forest of Ardenne lies on the Belgian side of the border. Joseph Haas and Roland Jost took over the sawmill for the purpose of manufacturing sustainable materials for industry and construction from the resources of this forest region. The Jost-Haas Group was expanded in 1999 by IBV of Vielsalm, Belgium, and in 2015 by Holz Schmidt of Cölbe. A total of 1.2 million solid cubic metres of timber are processed annually. In addition to the production of lumber, the production of wood pellets is an important part of the value creation today. Around 300,000 solid cubic metres of timber are processed annually at I.B.H. in Germany.
Remnants of the past
The Vogelsang International Place is located just a few kilometres north of Schleiden. This former Nazi “Ordensburg” was erected between 1933 and 1939, but it was never completed. The construction activity was ended by the Second World War. Today it is a place of remembrance and warns against the dangers of ideological delusion. At the same time it is an exhibition site for the impressive natural wonders of the Eifel. Heavy fighting took place in both World Wars in this and the surrounding forested areas in the border region. The Second World War in particular has left a lasting mark on the softwoods. At I.B.H., softwood is processed up to a diameter of 100 cm, smallwood on two canter lines and large logs on a log bandsaw. Spruces with diameters of around 90 cm or more endanger the cutting performance due to their contamination with balls, shrapnel or munition fragments. Smaller diameters may be affected if growth conditions are unfavourable. Also, metals in the form of nails or hunting munition are often found in younger trees.
In particular hard shrapnel made of steel or cast iron is very challenging for modern bandsaws. Loss of sharpness and thus increased maintenance work are the most frequent problems caused by this. A further problem is the possible development of heat and thus the annealing and weakening of the sawblade. In the worst case there is a risk of fire due to flying sparks. Likewise, ingrown metal particles can structurally weaken construction timber. However, this is not reconcilable with the company’s uncompromising quality standards.
Risk reduction strategies
I.B.H. has continually concerned itself with metal detection technology since its founding. “Our equipment is always state of the art. Only in this way can we deliver high quality at a fair price. That wouldn’t be possible with obsolete machines”, says Markus Haas, Member of the Board of Directors at the timber specialist. The tree trunk is examined by a metal detector integrated in the conveying equipment. Trees found to be contaminated with metal are recorded with the exact position and automatically sorted out. At I.B.H. these are completely recycled as waste timber, usually for generating wood pellets. However, expensive raw material is lost in the process, especially when processing large logs. Various solutions and makes have been used in the past, but the results were always unsatisfactory and led to production losses due to false alarms or undetected metals. The absolutely reliable and error-free detection of metals is therefore indispensable. This was then found in a graduated examination with metal detectors from the mechanical engineering company Mesutronic GmbH of Kirchberg im Wald in Lower Bavaria.
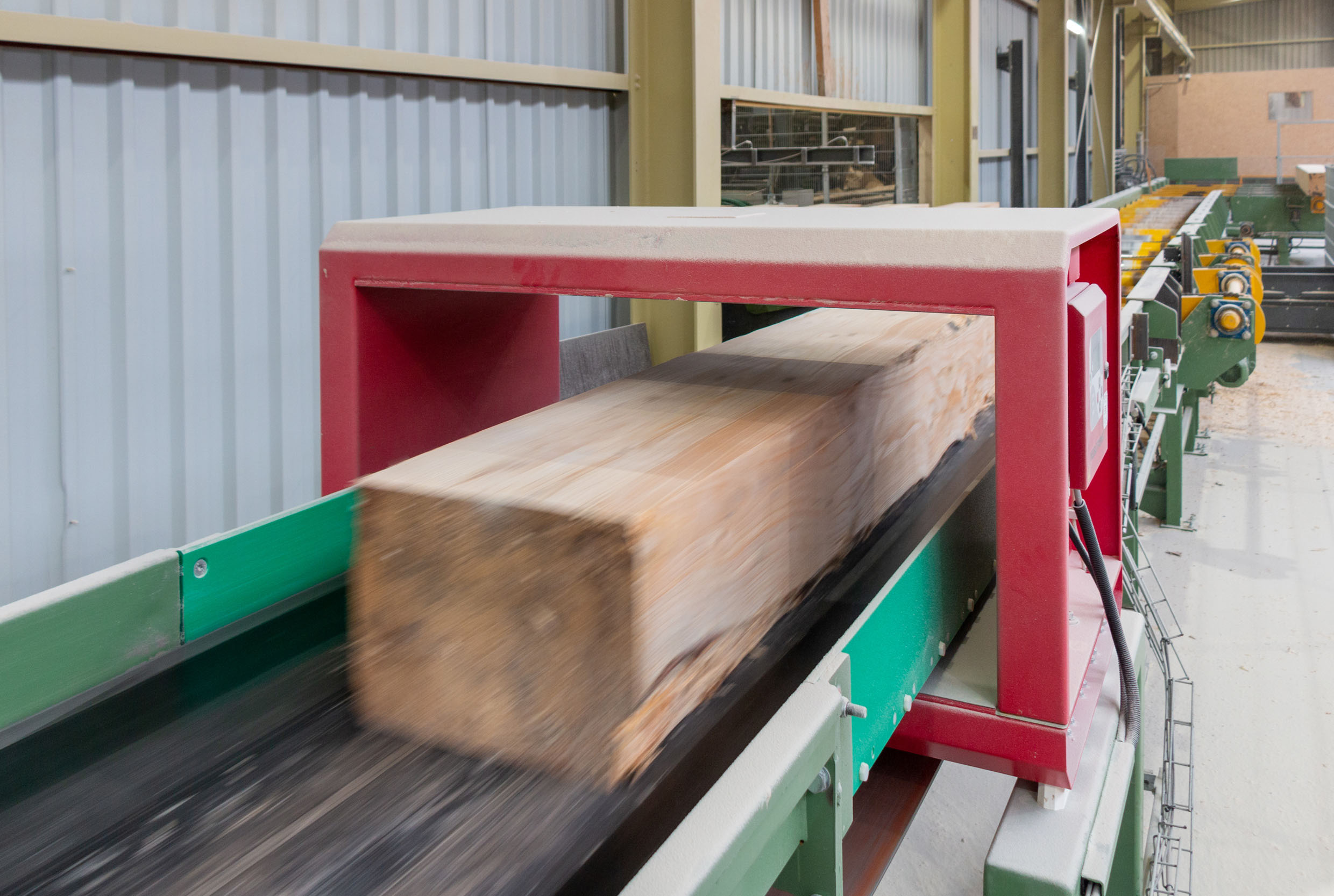
After pre-cutting in the log bandsaw, the square timbers are additionally examined by metal detector METRON 05 D
Only one option for freedom from metals
Following measurement and sorting in the log yard, the trunks first pass through the rotary bark stripper. This also removes metal particles on the surface together with the bark. Immediately after that, the examination for metallic foreign bodies takes place with the splinter detection device of the type METRON 05 CO. Here, contaminated trunks are detected with high precision, marked and subsequently ejected. The machine features excellent shielding against external influences due to electromagnetic and mechanical interference. This makes extremely stable operation possible. The octagonal aperture is also perfectly matched to the geometry of the conveying trough, allowing the size of the detection coil to be minimised.
After pre-cutting in the log bandsaw, the square timbers are additionally examined by a second metal detector from the METRON 05 D series. Since the beam diameter and thus the aperture size of the splinter detector are smaller here, even finer contaminants can be detected. This offers additional safety for the post-cutting and protects the high-performance sawing equipment. “Especially at times of wide fluctuations in the prices of round and square timbers, our customers need absolute reliability at least in their own production process. Since we are ourselves deeply connected with wood in our region, we are naturally only too pleased to make our contribution”, says Christian Boxleitner, Managing Director of Kirchberg-based specialists in foreign body detection.